Endüstriyel Kaplama Teknolojilerine Akademik Bir Bakış
- boranbezgen
- 3 Eki 2024
- 32 dakikada okunur
Güncelleme tarihi: 21 Kas 2024

ENDÜSTRİYEL KAPLAMA'YA GİRİŞ
Kaplama, bir malzemenin ortam şartlarında kullanılamadığı durumlarda veya bulunduğu ortama göre daha yüksek bir mekanik özellik istenmesi durumlarında uygulanmaktadır. Kaplamanın temel mantığı bir ana malzemenin optimum kalınlık oluşturulacak şekilde kaplama malzemesi -ki bu malzeme metal, plastik, seramik veya elektrolit çözelti olabilir- ile atomik yapışma sağlanarak ana malzemenin dış atmosfer koşulları ile bağını koparmaktır. Bu işlem ile dayanıksız malzemelerin daha dayanıklı malzemeler tarafından örtülmesi, dış etkenlerden korunması, istenilen özellikleri göstermesi amaçlanmıştır. Kaplama sektörü, ülke ekonomisi için yeni alanların ve imkanların son derece geniş olduğu bir sektördür. Bu sektör ile ihracat kalemleri artabilir, yeni istihdam alanları ile birlikte işsizlik düşebilir. Özellikle son zamanlarda yaşanan pandemi ile birlikte Çin Halk Cumhuriyeti’ndeki yüksek üretim kapasitelerinin dünyanın farklı bölgelerine kayması ve ülkemizin de bu üretim kapasitesinden yüksek bir pay alması için gerekli adımların atılması gerektiği uzmanlar tarafından ifade edilmektedir. Bu sektör potansiyeli yüksek olduğu kadar çevresel etkileri yüksek olan bir sektördür. Üretim sonrası atıklar, üretim amacıyla kullanılan çeşitli kimyasallar ve bol su tüketimi çevreye verilen en büyük zararı oluşturmaktadır. Kaplama teknolojisinin gelişmesinde ilk önce simyacıların bilimsel olmayan metotları ile başlanmış ancak daha sonra bilimsel çalışmalar ile birlikte amacını değiştirmiştir. Bugün uçaklarda kullanılan özel kaplamalar ile radar görünmezliğini, dinamik yükler altında çalışan bölgelerde kendini onaran kaplamalar, tıp alanında protezlerde kullanılan biyouyumlu kaplamalar ve yüksek sıcaklıklara dayanan termal bariyer kaplamalar ile katma değerli ürün ortaya koymaktadır.
KAPLAMA UYGULAMALARI
Kaplama prosesi farklı uygulama amaçları doğrultusunda gerçekleştirilmektedir. Bunlar;
Mühendislik amaçlı kaplamalar
Mühendislik amaçlı kaplamalar kendi içinde tribolojik (ısı+basınç) amaçlı, elektrik-elektronik amaçlı ve optik amaçlı olarak uygulanabilir. Kullanılan ana malzemeyi o ortama uygun daha yüksek özellikler sergileyen kaplama malzemeleri kullanılarak kaplama ile optimum çalışma şartlarının elde edildiği kaplamalardır.
Korozyondan koruma amaçlı kaplamalar
Özellikle metal malzemeler ve alaşımlar atmosferik koşullara ve sıvı kullanılan uygulamalarda korozyon, oksidasyon gibi etkenlere maruz kalmaktadır. Korozyona ve oksidasyona dayanıklı malzemeler ile kaplama sonucu atmosferik etkilerin asgari düzeyde tutulmasını sağlayan kaplamalardır.
Dekoratif amaçlı kaplamalar
Bu kaplamalar kullanılacak ana malzemenin parlaklık, renk, yansıtma gibi özelliklerinin değiştirilerek kullanıldığı ortama uygun hale getiren kaplamalardır.
Kaplamalar sadece kullanım amaçlarına göre değil kaplama malzemesine veya kaplanacak ana malzeme türüne göre de farklılıklar göstermektedir.
METALLERİN METALLERLE KAPLANMASI
ELEKTROLİTİK KAPLAMA
Elektrolitik metal kaplama yönteminde katot malzeme, anot malzeme elektrolit ve bunlara uygun bir banyo kullanılmaktadır. Ana malzemesi metalik veya metalik olmayan malzeme kullanılabilir. Elektrolit, kaplanacak metali iyonik halde içeren sulu bir çözeltidir. Kaplama metalini bu çözelti içinde bulundurmanın en kolay yolu o metalin basit bir tuz çözeltisini kullanmaktır. Bu işlem ana metalin katot ve kaplama metalinin anot olarak kullanıldığı elektrolitik çözelti içerisine daldırılması ile sağlanır. Ana metal elektrolit içerisine daldırıldığında elektriksel kaynaklar (transformatör ve rektifiye) gerekli olan düşük gerilimi (doğru akımı) ayarlar. Banyolarda (tanklarda) ph değeri çok önemlidir. Çözeltiler asidik, bazik ve nötr olabilir. Basit metal tuzlarının kullanımında elektrolit asidik olmalıdır. Asidik olmadığı durumlarda kaplama metali hidroksit halinde çöker. Siyanür banyoları ise baziktir. İşlem sırasında sulu çözelti içindeki iyonlar katoda giderek element halinde birikir ve kaplama gerçekleşir.[1] Elektrolitik kaplamada anot metali olarak çinko, bakır, krom, kadmiyum, nikel, gümüş, kalay, pirinç ve altın kullanılmaktadır.

BAKIR KAPLAMA
Bakırın elektrolitik yolla kaplanması çeşitli banyoların kullanılması ile gerçekleştirilir. Bu banyolar; asit-sülfat banyoları, alkalin banyosu ve siyanürlü alkalin banyosu, pirofosfat ve fluoroborat banyolarıdır. Genel kullanımın dışında klorür ve tartarat banyoları da kullanılmaktadır. Metalik bakır dibe çöker ve bu anot ucu oluşturur. Proses sırasında bakır sülfatın fazlası atılmalıdır. Bu farklı yöntemlerle gerçekleştirilebilir. Belirli periyotlarda çözelti alınarak yerine su veya sülfürik asit eklenerek istenilen konsantrasyon elde edilir veya çözelti içerisine kurşun elektrotlar daldırılarak bakır sülfatın aşırısı giderilerek asit elde edilir. Daha basit bir yöntem olarak ise alınan çözelti banyodan atılır. Asitli bakır kaplama çözeltilerine daldırma ile yapılan kaplamanın yapışma mukavemeti düşüktür. Eğer kaplamada iyi bir yapışma gerekiyorsa dağıtma özelliği yüksek olan siyanürlü kaplama tercih edilmektedir. Asitli kaplamaların avantajı ise yüksek yüzey düzeltme kabiliyetine sahip olmalarıdır. Siyanürlü çözeltinin bu özelliği kazanması için ters akım uygulamak veya katkı maddeleri eklemek gerekmektedir.

Bakırın kaplama malzemesi olarak kullanılması ile elde edilmek istenen mekanik ve fiziksel özellikler şöyledir; sürekli bir yüzey oluşturması, korozyona karşı dayanıklılığı, elektrik iletkenliği, lehimlenebilirliği, sertleşmeye karşı direnci, yumuşaklık, parlatma kolaylığı, diğer metallerde üst kaplama kolaylığı sağlaması ve dekoratif bir görüntü elde edilmesidir. Genellikle çok katmanlı kaplamaların birinci katında bakır kullanılmaktadır. Bunun nedeni atmosfere açık yerlerde korozyona dirençli olsa bile kararmasıdır. Özellikle dış etkenlere açık nikel ve krom kaplı parçaların üzerine iki kat bakır kaplama yapılmaktadır. [3] Düşük karbonlu çeliklerin bakır ile kaplanmadan önce bir ön işlemden geçirilmesi gerekmektedir. Düşük karbonlu çeliğe durulama uygulandıktan sonra %4-10 H2SO4 veya %5-25 HCl aside daldırılır. Bu işlem anodik temizlemedir. Her bir banyodan sonra mutlaka durulama gerçekleştirilmelidir. Bu ön işlemden sonra kaplama prosesine devam edilmektedir. Yüksek karbonlu düşük alaşımlı çeliklerde bu ön işlemler biraz daha kompleks bir hal almaktadır. Çok kademeli bir durulama, aside daldırma ve anodik temizleme işlemlerinde sonra kaplama gerçekleştirilmektedir.
Kaplama kalınlığı 3 ile 8 mikron arasında isteniyorsa ve doğrudan çelik üzerine bakır kaplama istendiğinde bakır siyanür çözelti ile kaplanmalıdır. Kaplama kalınlığı 10 mikronun üzerinde isteniyorsa, bu istenen fazla kaplama için yüksek konsantrasyonlu asidik çözelti uygulanır.
ÇİNKO KAPLAMA
Çinko en çok baz metallerin kaplamasında kullanılmaktadır. Kaplamada siyanürlü alkali çözelti ve siyanür içermeyen alkali çözelti olarak kullanılmaktadır. Asidik elektrolitiklerde kullanılmaktadır. Asidik banyolarda fluoroborat, perklorat, sulfamat ve pirofosfattan oluşabilir. Ancak genle olarak sülfat, klorür veya ikisinin karışımı kullanılmaktadır. Çinko kaplama korozyona karşı oldukça dayanıklıdır. Esnek, kaplama yöntemlerinin basit ve ucuz olması, iyi yapışma sağlaması avantajlarıdır. En önemli dezavantajı zehirleyici etkisi olduğundan gıda ürünlerinin bulunduğu yüzeylere uygulanamamasıdır. Yapışma kabiliyetinin artırılması kaplama öncesi mekanik parlatma işlemi ile gerçekleştirilebilir. Korozyon direnci kaplama kalınlığı ile azalmaktadır. Bu nedenle kaplanacak ana metalin kullanım yerine göre kaplama kalınlığı belirlenmektedir. Bu kaplama kalınlığı 5-50 μm aralığında değişmektedir. Elektrolitik çinko kaplamada hangi banyo çözeltisi kullanılırsa kullanılsın parçaların yüzey temizleme işlemleri dikkatli bir şekilde gerçekleştirilmelidir. Kaplanacak parça kaynak bölgeleri bulunduruyorsa asidik yağ alma işlemine alınmalıdır. Çinko kaplamada elektrolit çözelti %100 saflıkta çinko olmalıdır. Kaplama işleminden sonra pasivasyon işlemi yapılmalıdır. Pasivasyon işlemi kaplama üzerinde kalabilecek karbonları arındırmadır. Nitrik asit banyosuna daldırılarak bu işlem gerçekleştirilir. Her banyodan sonra mutlaka durulama yapılmalıdır. Kaplamanın renklendirilmesi istendiğinde uygun çözeltilerin içerisinde belirli sürelerde bekletilerek istenen renk çinko kaplamaya uygulanabilmektedir. Tüketilen çinkonun %50 si galvanize edilmiş çelik yapımında kullanılmaktadır.
NİKEL KAPLAMA
Nikel kaplama dekoratif, mühendislik ve elektrikle biçimlendirme amaçlı yapılan kaplamadır. Dekoratif amaçla kaplanan nikel çözeltisi mühendislik veya elektrikle biçimlendirmede kullanılan çözeltiden farklıdır. Parlak nikel kaplama genellikle dekoratif amaçlı kullanılmaktadır. Kaplanacak ana metalin yüzey düzgünlüğü ne kadar düzgün olursa kaplamanın en üst kademesi de o kadar iyi olur. Nikel kaplama korozyona dayanıklı değildir.
Nikelle kaplanmış bir parça daha sonra farklı metaller ile kaplanabilmektedir. (Krom, altın, gümüş, pirinç vs.) Parlak nikel üzerine yüksek poroziteli dekoratif krom kaplama ile korozyon direnci sağlanabilir. Genelde nikel kaplama çözeltisi asgari %98 oranında saflık içermelidir. Nikel kaplamada banyo yöntemleri şunlardır; Mat nikel-yarı parlak nikel, parlak nikel, nikel sülfamatlı banyo, nikel floboratlı, akımsız nikel kaplama, satine kaplama, nikel profosfatlı banyo ve siyah nikel kaplamadır. Kullanılan çözelti çeşitleri nikel sülfat (NiSO4.7H2O), nikel sulfamat (Ni(SO3NH2)2), nikel klorür (NiCl2.6H2O) ve bazik nikel karbonattan (NiCO3.Ni(OH)2) oluşmaktadır. Bu nikel tuzlarına ek sodyum sülfat (Na2SO4), magnezyum sülfat (MgSO4), amonyum klorür (NH4Cl), sodyum klorür (NaCl), sodyum sitrat (Na3C6H5O7.11/2H2O) ve borik asit (H3BO3) gibi ek tuzlar da içerebilir. Nikel çözeltilerinde demir ve çinko kaplama kalitesini bozmaktadır. Nikel elektrik kontakların kararma direncini sağlama ve çeliği galvanik olarak koruyamayan soy metallerde alt kaplama olarak kullanılmaktadır. Mühendislik kullanımında nikel kaplama mat görünümde olmaktadır. Ana metale tokluk ve süneklik, korozyon direnci, yük dayanımı, aşınma direnci gibi fiziksel ve mekanik özellik kazandırılmaktadır. Nikel kaplamada kompleks parçaların kaplanması sırasında yüksek akım yardımı ile gerçekleştirilmektedir. Nikel banyolarında akımın küçük bir miktarı hidrojene gitmektedir. Bu nikelin verimliliğini düşürmektedir. Nikel kaplama tabakasının yapısını banyo sıcaklığı, akım yoğunluğu ve kaplanacak yüzeyin pürüzlülüğü etkilemektedir. [4]
KROM KAPLAMA
Krom yüksek ergime sıcaklığına sahiptir. Krom başlıca şu özelliklerden dolayı kaplama malzemesi olarak tercih edilmektedir; Serttir, parlaklığını kaybetmez, aşınmaz, korozyona uğramaz, kükürtlü bileşimlere, kimyasal etkilere ve ısıya dayanıklılığıdır. Bu özellikler krom kaplamanın, ana metalin mekanik özelliklerini iyileştirmek amaçlı sert krom kaplama yöntemiyle mühendislik uygulamalarında ve dekoratif uygulamalarda kullanılmasına neden olur. Özellikle otomobil sektöründe sıkça kullanılmaktadır. Krom sıcak sülfürik asitle çözünmesi ile oluşan tuz çözeltileri olarak banyolarda kullanılmaktadır. Kaplama öncesi yüzey temizleme işlemi galvanizleme işleminde oldukça önem kazanmaktadır. Krom kaplama öncesi temizlik sırasında 65-70 ℃ sıcaklıkta su ile %5-10 oranında karıştırılan çözeltide 5-15 dakika bekletilmesi ile gerçekleştirilir. Temizlemede etkin tuzlar ve tuzların yanında emülgatör ve inhibitörlerde kullanılmaktadır. Kaplama tuz çözeltisi kromik asit (CrO3) ve sülfürik asit (H2SO4), karışımından elde edilmektedir. [5]

KADMİYUM KAPLAMA
Kadmiyum çelik, bakır, demir, diğer metal ve alaşımlarda korozyondan korunma amacı ile kullanılmaktadır. En büyük avantajı demire karşı anodik özellik göstermesidir. Bu özelliği kaplamanın çizilmesi veya kazınması durumunda dahi çeliği korumaya devam etmesini sağlamaktadır. Atmosferik koşullarda çinkoya oranla dayanıklı olması diğer bir avantajıdır. En büyük dezavantajı kimyasal korozyona direncinin diğer kaplamalara göre daha düşük olmasıdır. Kimyasallar ile oluşturduğu tepkimeler bu kaplamanın gıda ürünlerinin bulunduğu ortamlarda zehirlenmeye yol açmasına neden olur. Bu nedenle bu alanlarda kullanılmamaktadır. Kadmiyum düşük sürtünme katsayısı, iyi elektrik iletkenliği, korozyona uğraması sırasında daha az ürünler açığa çıkartması, lehimlenebilirliği ve kromatlanabilmesi açısından üstün özellikleri bir arada barındırmaktadır. En çok elektronik cihazların iç parçalarının kaplamasında kullanılmaktadır. Banyo çözeltisinde kadmiyum oksit (CdO), kadmiyum siyanür (Cd(CN)2), kadmiyum sülfat (CdSO4.8/3H2O), potasyum kadmiyum siyanür (K2Cd(CN)4) ve kadmiyum sodyum siyanür (CdNa(CN)3) gibi tuzlar kullanılmaktadır. [6]
KALAY KAPLAMA
Kalay aşınma ve asit dayanımı gibi özelliklerinin yanı sıra gıda ürünlerinin kullanıldığı alanlarda zehirlenmeye sebebiyet vermemesi açısından kaplama malzemesi olarak kullanılmaktadır. Kalay oda sıcaklığında hava ve sudan etkilenmez. Kalay zayıf organik ve anorganik asitlerden az etkilenirken organik asitlerden hiç etkilenmez. Kalay kaplama asidik ve alkali çözeltiler kullanılarak gerçekleştirilmektedir. Asitli kalay banyosu temel tuz ve kalay sülfat (SnCl2) karışımından oluşur ve yüksek akım kullanılabilmektedir. Alkali banyo çözeltisi temel tuz ve sodyum stannat (Na2SnO3.3H2O) karışımından oluşur ve kaplama ince tanelidir. [4]
GÜMÜŞ KAPLAMA
Gümüş kaplama süsleme amacının yanında elektrik devrelerinde ilgili parçaların kaplanması amacıyla kullanılmaktadır. Hava ile temasta oksitlenmemesi ve çok güçlü elektrik i8letkenliği bu alanlarda kullanılma sebebidir. En büyük dezavantajı korozyona diğer metallere oranla daha az dayanıklı olması ve zamanla sülfit oluşumuna bağlı olarak kararmasıdır.[1] Gümüş kaplama banyolarında çözelti olarak metal siyanürlü gümüş tuzları kullanılır. Banyo çözeltilerinde sodyum veya Potasyum gümüş siyanür, Sodyum veya potasyum karbonat ve sodyum veya potasyum siyanür kullanılmaktadır. Banyo işlemi üç aşamada gerçekleştirilir. Bunlar; ön gümüş kaplama, mat gümüş kaplama ve parlak gümüş kaplamadır. Gümüş tanecikleri ne kadar küçük olurlarsa o kadar parlaklıkları artar. Bazı banyolarda parlaklık için parlatma tuzları çözeltilere eklenmektedir. Katot akımının yüksek olması gümüş kaplamanın gri olmasına neden olabilir. [4]
ALTIN KAPLAMA
Altın kaplama, altının kolay biçimlendirilmesi, lehimlenebilmesi, yüksek elektrik iletkenliği, korozyona uğramaması ile birlikte aşınma ve kararma problemleri olmamasından tercih edilmektedir. Altın kaplama malzemesi olarak gümüş, pirinç, çelik gibi farklı metallerde kullanılmaktadır. Altın Dekoratif olarak ve elektronik parçalarda kaplama malzemesi olarak tercih edilmektedir.[1] Altın kral suyu (HNO3+3HCl) ile tuz çözelti haline getirilerek banyolarda kullanılır. Banyolarda bu tuz siyanürlü ve serbest siyanürlü olarak kullanılmaktadır. Siyanürlü altın banyosunda elektrolit olarak altın klorür (AuCl3) veya altın siyanür (AuCN) kullanılmaktadır. Soğuk ve sıcak altın banyolarında anot olarak çözünür altın veya çözülmeyen çelik kullanılır. İnce altın taneleri için paslanmaz çelik sac kullanılır. [4]
ALAŞIM KAPLAMA
Farklı iki metalin alaşımlarının elektrolit çözeltisinde kullanılarak kaplamanın gerçekleştirilmesidir. Çinko-nikel, çinko-demir, çinko-kalay, çinko-kobalt ve çinko-mangan fosfat kaplamada kullanılan çinko alaşımlarıyken; Bakır-nikel-krom kaplama, kurşun-kalay, nikel-kalay, nikel-demir, gümüş-kadmiyum, tungsten alaşım ve en çok kullanılan bakır-çinko (pirinç) kaplama diğer alaşım kaplamalardır. [1]
SICAK DALDIRMA
Sıcak daldırma, yüzey temizleme işlemleri tamamlanmış demir veya çeliği eriyik halde bulunan çinko banyosuna daldırarak yapılan kaplama işlemidir. Eriyik çinko yaklaşık 450 ℃ de havuzlarda tutulur. Ana metalin daldırılması ile metalürjik bağ gerçekleştirilir. Önemli avantajlarından dolayı sıcak daldırma galvanizleme tercih edilmektedir. Bunlar:
Çizilse veya aşınsa dahi tüm çinko tükenene kadar korozyondan korur.
Uzun ömürlüdür.
Kaplama sonrası bakım-onarım gerektirmez.
Diğer kaplamalara göre ekonomiktir.
Elektrolit çözeltilerde olduğu gibi çevreye zarar veren çözeltiler yoktur.
Ana metalin tüm girinti ve çıkıntılarını aynı kalınlıkta kaplayarak homojen bir kaplama elde edilmesidir.
Bu özellikleri ile sıcak daldırma yapı çeliklerinde, bağlantı elemanlarında, otomotiv ve uçak sektöründe oldukça fazla kullanılmaktadır. [7] Kaplama kalınlığını etkileyen önemli faktörlerden birisi çeliğin içerdiği silisyum miktarıdır. Silisyum miktarının ya %0.03 den az olması ya da %0.15-0.25 arasında olması istenir. İdeal bir kaplama kalınlığı için karbon oranının %0.25 den az, fosfor oranının %0.04 den az ve mangan oranının %1.35 den az olması istenir. [8] Sıcak daldırma işlemi ile gerçekleştirilen alüminyum kaplama işleminde karmaşık geometriye sahip ana metallerin homojen kaplandığı ve kaplama kalınlığının banyo sıcaklığı, bekletme ve tavlama süresi ile korozyona karşı korumada kalaya kaplamaya alternatif olduğu görülmektedir. [9]
TERMAL PÜSKÜRTME İLE KAPLAMA
Detonasyon püskürme ile kaplama
Bu püskürtmede sevk gazı farklı gazların tabanca içerisinde karışması ile gerçekleştirilir. Kullanılan gazlar azot gazı, asetilen gazı ve oksijen gazıdır. Detonasyon püskürtmede gaz birkaç saniyelik aralıklarla elektrik kıvılcımı verilerek patlatılır. Gazın patlatılması sırasında toz metaller ısıtılır. Toz metaller gaz ile beraber yakaladıkları yüksek bir ivme sayesinde tabanca içerisinden ana metale doğru püskürür. Bu yüksek kinetik enerjili toz metalleri ana metal üzerine çarptıklarında kinetik enerjileri ve gazlarda aldıkları ısı ile tekrar ısı açığa çıkartırlar. Bu durum ana metal ile kaplama metalinin mikrokaynak düzeyinde birleşmelerine yol açar. Detonasyon uygulaması 50-60 rockwell sertliğinden yüksek sertlikteki tüm metaller kaplanabilmektedir. Metalik olmayan ana malzemeler gazın yüksek erozyon oluşturmasından dolayı kaplanamamaktadır. [14]
Plazma püskürtme ile kaplama
Plazma püskürtme yönteminde farklı özellikler malzemeye kazandırılabilmektedir. Bunlar ısıl bariyer oluşturma, oksidasyon dayanıklılığı, aşınma ve korozyon direnci sağlaması ve düşük maliyetli olmasıdır. Plazma kaplama havacılık-otomotiv endüstrisinde, tıbbi cihazlarda, tarım makinelerinde ve iletişim cihazlarında kullanılmaktadır. Plazma püskürtmede seramik malzemeler ve yüksek ergime noktasına sahip metal ve alaşımlar ana malzeme olarak kullanılmaktadır. Plazma katot ile anot arasındaki ark ile sağlanmaktadır. Katot olarak tungsten kullanılırken anot olarak bakır kullanılır ve su ile soğutulur. Burada oluşan ark ile gaz iyonize olarak plazma durumuna geçer. Plazma gazını oluşturmak için şu gazlar kullanılır ve iki grupta toplanırlar. İlk grupta argon ve helyum gazları bulunurken ikinci grupta azot ve hidrojen gazları kullanılmaktadır. Kullanılacak gaz karışımı plazmanın entalpisini ve hızını artıracak şekilde hazırlanmalıdır. Püskürtme sırasında hız 300-550 m/s arasında değişmekte ve kaplama kalınlıkları da 0.05-0.50 mm arasındadır. Bu kaplamaların dayanımları ise 34-69 MPa olarak ölçülmüştür. Kaplama işlemi mekanik yollarla gerçekleştiğinden kaplama öncesi ana malzeme yüzeyinin pürüzlendirilmesi daha kaliteli bir kaplama elde edilmesini sağlar. [14]
Yüksek hızlı oksi-yakıt püskürtme (HVOF)
Bu yöntem mükemmel mekanik özelliklerin ana malzemeye kazandırılmasında kullanılmaktadır. Özellikle korozyona ve aşınmaya maruz kalınan ortamlarda bu kaplama oldukça faydalı olmaktadır. Yüksek hızlarda ve düşük sıcaklıklarda dayanımlı kaplama oluşturulmaktadır. Bu yöntemde yüksek bir basınç odası içerisindeki gazların tek bir nozulda birleşerek yüksek hızlarda ana malzeme üzerine püskürtülmesi ile gerçekleştirilmektedir. Burada oluşan termal püskürtme bazı parametrelere bağlıdır. Bunlar; hız, sıcaklık, katılaşma derecesi, alt tabaka malzemesi ve alt tabak sıcaklığıdır. [14]
KAPLAMA KALNLIĞINI ETKİLEYEN FAKTÖRLER
Akım Yoğunluğu: Akımın iki farklı etkisi vardır. Akım yoğunluğu artarsa kristalleşme hızı artar ve ince taneli bir yapı sağlanır. Yoğunluğun gereğinden fazla olması kaplama fakirleşir ve homojen yapı elde edilemez.
Sıcaklık: Sıcaklık difüzyonu artırır ve ince taneli bir yapı meydana getirir. Sıcaklığın artması ile polarizasyon azalır ve kristal taneleri iri yapılı oluşur. Kaplama türüne göre uygun sıcaklık değerleri seçilmelidir.
Metalin ve Elektrolitin Yapısı: Kompleks tuzların elektroliziyle elde edilen kaplamalar daha üstün özellikler sergilemektedir.
Kaplama öncesi temizlik ve kontrol: Kaplanacak parça yüzeyinin temizliği, pas, yağ, talaş gibi kaplama kalitesini etkileyebilecek etmenler kaplama öncesi parçadan arındırılmalıdır. Bu temizlik kimyasal veya mekanik yolarla gerçekleştirilebilir.
Filtrasyon ve karıştırma: Kaplamada kullanılan çözeltiler yani anot malzeme %100 saf değildir. Bu durum zamanla banyo tankının dibinde bir anot çamuru katmanı oluşmasına neden olur. Kaplamanın sağlığı açısında belirli periyotlarda çözeltinin filtrelenmesi veya çamurun erken çökmemesi için karıştırma uygulanmalıdır.
Konsantrasyon: Optimum çözelti konsantrasyonu kristallerin ince taneli olması açısından oldukça önemlidir. Karakteristik bir kriterdir.
Ph Etkisi: Çözeltide kullanılan tuzlar asidik veya alkali olabilir. Bu durumda çözelti ideal ph değerinde tutulmalıdır.
Kaplama Gücü: Kaplamanın aynı kalınlıkta ve parçanın girintilerine ve ince detaylarına ulaşmasının yanı sıra kaplama kalınlığının ince olması istenir.
Tanklar: Temizleyici ve alkali çözeltiler barındıran tankların malzemeleri çelik olabilir ancak sülfürik asit ve kromik asit içeren tankların malzemeleri kurşun kaplanmış çelik olmalıdır. Nötr veya diğer asit banyoları için kauçuk kaplama tanklar kullanılmalıdır.
ELEKTROLİZ KAPLAMANIN ÇEVREYE ETKİLERİ VE İŞ SAĞLIĞI
Elektrolitik kaplamada çevre etkeni oldukça önemlidir. Kaplama banyolarında kullanılan çözeltilerin bileşimleri ve durulamalarda kullanılan temiz suların kirlenmesi gibi etkenler çevrenin kirlenmemesi için ek önlemler almayı gerektirmektedir. Kaplama prosesinde en yüksek maliyet yaklaşık %50 ile enerji ve %40 ile kimyasal malzemelerdir. İşletmeler çevre için gerekli önlemleri öncelikle bu maliyetli girdileri azaltmak için kullanmalıdırlar. Banyolarda kullanılan kirletici kimyasallar en büyük sorunu teşkil etmektedir. Bunların başında krom 6, kadmiyum ve siyanür yer almaktadır. Bu kirleticiler gerekli atık yönetimi uygulanmadığı taktirde yer altı sularını kirletmektedir. Kaplama prosesinde alınabilecek önlemeler şu şekilde sıralanabilir: [1]
Tehlikeli kimyasal kullanımın optimum gerçekleştirilmesi,
Sıcak banyolarda enerji tasarrufuna yönelik uygulamalar konulması,
Banyo ömrünün uzatılması
Kimyasal temizlik yerine uygulanabilecek fiziksel temizliklerin uygulanması
Banyo analizlerinin düzenli aralıklarla yapılarak veriminin uzatılması
Süzüntünün azaltılması
Durulama suyunun ideal kullanılması
Kirleticilerin kullanılmadığı alternatif proseslerin kullanılması
Atık su haline gelen banyo çözelti ve sularının içerisindeki hammaddenin geri kazanımı
Atık su arıtma
Kaplama sektöründe kimyasalların kullanılması iş sağlığı açısından önemli tedbirler alınmasını gerektirir. İnsan sağlığı açısından zehirleyici ve aşındırıcı kimyasallar karşısında koruyucu donanımların işletmelerde önemle kullanılmaları gerekmektedir. Yapılan araştırma 2012-2017 yılları arasında metal kaplama sektöründe yaralanma ile sonuçlanan 1280 ve uzuv kaybı ile sonuçlanan iş kazası sayısı 10 dur. [10]
PLASTİKLERİN METAL KAPLANMASI
Yalıtkan malzeme kaplamaları uzun yıllardır yapılan ve çoğu sektörde kilit rol oynayan bir kaplamadır. Ancak kaplama ve ana malzeme yani metal-polimer arasında bağlanma kuvvetlerinin düşük olması sorun çıkarmaktadır. Bu durum bir ara katman ile giderilmektedir. Bu kaplamalar özellikle tıp alanında, elektrik ve enerji uygulamalarında, uçak ve uzay endüstrisinde oldukça önemli bir yer tutmaktadırlar. Özellikle sürtünmeye maruz kalan ve bu nedenle verimliliğin ortadan kaldığı durumlarda kullanışlıdır. Plastikler genellikle ince film üretim teknikleri, akımsız metal kaplama ve püskürtme yöntemleri gibi yöntemler ile kaplanmaktadır. Plastiklerin kaplanmasında ana malzeme olarak genellikle Akrilonitril butadien stiren (ABS), Polipropilen (PP), Polisulfan (PSU), Teflon (PTFE), Polikarbonat (PC), Polistiren (PS), General purpose polystyrene (GPPS), Polibütilen tereftalat (PBT), Stiren akrilonitril (SAN), ve Mineral takviyeli naylon (MNR) ve bu plastiklerin karışımları kullanılmaktadır. Plastiklerin metal kaplanması sağladığı hafiflik, tasarım esnekliği, düşük maliyet, seri üretim kolaylığı, elektromanyetik koruma sağlaması, elektrik iletkenliği kazandırılması, darbeler karşı direncin artması ve sürtünme özelliklerinin iyileştirilmesi yönünden tercih edilmektedir.
AKIMSIZ KAPLAMA
Bu yöntemde elektrik akımı kullanılmadan, ana malzemenin elektrolite daldırılır. Elektrolit içerisindeki indirgeyici maddeler yardımıyla ana malzeme üzerine kaplama malzemesi indirgenir. Son yıllarda akımsız kaplama yöntemi ile plastik veya plastik matrisli kompozitlere metal kaplama işlemi önem kazanmıştır. Plastiklerin metal kaplanmasında genellikle nikel ağırlıklı çözeltiler kullanılmaktadır. Kaplamada nikel ağırlıkça %88-95 oranında bulunur. Yani nikel yabancı bazı maddeleri de ana malzemeye bağlamaktadır. Bunlardan biri olan fosfor bağlandığında metalik cam adı verilen amorf bir yapı oluşturlar. Ana malzeme olarak genellikle Akrilonitril butadien stiren (ABS) veya ABS-Polikarbon (PC) karışımları kullanılmaktadır. Kaplamanın genel amacı dekoratif bir görünüm vermektir. Ancak bazı mühendislik uygulamalarında sürtünme katsayısını düşürmek, lehimlenebilirliği sağlamak, korozyon koruması sağlamak amaçlanmaktadır. Kaplama kalitesinin istenen seviyede gerçekleştirilmesi için yapışkan metal tabakasının elde edilmesidir. Yapışkan metal tabaka ne kadar kaliteli elde edilirse kaplama kalitesi o kadar azami olacaktır. [41]
İNCE FİLM ÜRETİM İLE KAPLAMA
Ana malzeme ve kaplama malzemesi arasındaki bağlanma gücüne bağlı olarak üç farklı film mekanizması bulunmaktadır. Bunlar; tabaka-tabaka büyüme mekanizması (van der merwe), üç boyutlu nükleasyon (volme-weber mekanizması) ve tek tabaka adsorpsiyonu (stranski-krastanov mekanizması) mekanizmasıdır.
Fiziksel buhar biriktirme (PVD)
Bu yöntemde yüksek vakum altında buharlaştırılan metal malzemenin plastik malzeme üzerine biriktirilmesi ile gerçekleştirilmektedir. Vakumun oluşturulma sebebi buharlaşan kaplama malzemesinin iyonlaşana diğer parçacıklara çarpmadan doğrudan ana malzeme üzerine birikmesi içindir. Burada buharlaşma atomik düzeyde gerçekleşmektedir. Yüksek biriktirme hızları, ana malzemenin mikro yapısına zarar vermemesi, uygun toleranslarda kaplama kalınlığı ve özellikle geniş yüzeyli ve ısıya dayanıklı malzeme kaplamalarında PVD yöntemi ön plana çıkmaktadır. Yöntem uygulanırken yüksek iç gerilmeler meydana gelmektedir. Bunun nedeni uygulamada kullanılan malzemelerin koşullarıdır. Özellikle refrakter kaplama malzemeleri ve düşük ana malzeme sıcaklıkları bunun ana nedenidir. Kaplama malzemesi olarak Ti, Cu, Cr, Zr, Al, Ag, Ni-Cr gibi alaşımlar ve malzemeler kullanılmaktadır, PVD kaplama yönteminde işlem sıcaklıkları 250-450 ℃ arasında değişmektedir. Ana malzeme olarak Poliimid, Polikarbonat, Polistiren, Nylon ve Teflon kullanılmaktadır. Kaplama malzemelerinin buharlaşma sıcaklıkları 300-4000 ⁰K arasında değişmektedir. [12] [31] [42]
Kimyasal buhar biriktirme (CVD)
Kimyasal buhar biriktirme (Chemicals Vapour Deposition-CVD) yönteminde kaplama olarak kullanılacak metalin bir bileşiği veya bu metalin kompleksi tercih edilmektedir. Ana malzeme olarak Akriklik (PMMA) ve Polikarbonat (PC) gibi plastikler kullanılmaktadır. [44] Kaplama metal, yüksek vakum altında ısıl bozunmaya uğratılır. İşlem sırasında yüksek sıcaklıklar (1000 ℃) elde edilir. Metal bileşiği ısıya uğradığında bozunma ile birlikte metale dönüşür ve ana malzemenin yüzeyine ince metal filmler oluşturacak şekilde yapışır. Bu kaplamanın en büyük avantajı her yerde aynı kaplama kalınlığının elde edilerek homojen bir kaplama oluşturmasıdır. Düşük basınçlarda gerçekleştirilen reaksiyonlarda; difüzyon, eş biçimlenmeyi yükseltir ve biriktirmenin veriminin yükseltir. Kimyasal biriktirme çeşitleri şunlardır: [11]
Atmosferik basınçlı kimyasal biriktirme (APCVD)
Alçak basınçlı kimyasal buhar biriktirme (LPCVD)
Metal-organik kimyasal buhar biriktirme (MOCVD)
Plazma destekli kimyasal buhar biriktirme (PECVD)
Lazer kimyasal buhar biriktirme (LCVD)
İyon kaplama biriktirme
Bu kaplamada belirli periyotlarda enerji yüklü parçacıklar ile ana malzeme üzerinde bir bombardıman gerçekleştirilir. Bu bombardıman sırasında kullanılan yüksek enerjili parçacıklar inert veya reaktif gaz iyonları ve kaplama malzemesinin iyonlarıdır ve bu iyonlar zamanla ana malzeme üzerinde bir film tabak oluşturarak büyür. Bu işlem bir vakum ortamında ve elektron tabancı ile gerçekleştirilir. Bu işlem ile birlikte plastiklerin ve yarı iletken malzemelerin alüminyum (Al), gümüş (Ag), altın (Au) gibi metallerle kaplanarak iletken duruma getirilmesinde kullanılmaktadır.
İyon kaplama biriktirme
Bu kaplamada belirli periyotlarda enerji yüklü parçacıklar ile ana malzeme üzerinde bir bombardıman gerçekleştirilir. Bu bombardıman sırasında kullanılan yüksek enerjili parçacıklar inert veya reaktif gaz iyonları ve kaplama malzemesinin iyonlarıdır ve bu iyonlar zamanla ana malzeme üzerinde bir film tabak oluşturarak büyür. Bu işlem bir vakum ortamında ve elektron tabancı ile gerçekleştirilir. Bu işlem ile birlikte plastiklerin ve yarı iletken malzemelerin alüminyum (Al), gümüş (Ag), altın (Au) gibi metallerle kaplanarak iletken duruma getirilmesinde kullanılmaktadır.
SIÇRAMALI BİRİKTİRME İLE KAPLAMA
Bu yöntemde enerji yüksek kinetik enerjiye sahip kaplama malzemesinin ana malzemeye çarparak ısı enerjisi açığa çıkarması ile gerçekleştirilmektedir. Bu yüksek kinetik enerjiye sahip parçacıklar genellikle kaplama malzemesinin iyon, elektron veya atomlarıdır. Bu işlem vakum altında veya düşük basınçlı gaz ortamda gerçekleştirilmektedir. Bu yöntem ile genellikle polimerlerin üzerine yansıtıcı bir kaplama yapılmasında kullanılmaktadır. Sıçratmalı biriktirme 4 farklı şekilde gerçekleştirilmektedir: [42]
DC Sıçratma: Kaplama malzemesinin bulunduğu bir katot elektrottan ve ana malzemenin bulunduğu bir anot elektrottan meydana gelmektedir. Haznesinde basınçlı gaz doldurulur ve uygun akım uygulanarak plazma meydana getirilir. Bu plazmanın oluşturduğu sıcaklık ile kaplama malzemesi katottan anot uca doğru sıçratılır.
RF Sıçratma: Kaplama malzemesi manyetik alana tabi tutularak bir iyon bombardımanı sonucunda ana malzemeye sıçratılarak gerçekleştirilmektedir. Manyetik alan negatif voltaj ile oluşturulmaktadır. Oluşturulacak negatif voltaj için değerler 10-3-1 Torr ve 100V-1kV arasındadır. İyon bombardımanın sırasında oluşabilecek kirliliğin engellenmesi için argon gazı kullanılmaktadır. Bu sistem yüksek maliyet ve düşük uygulama hızı nedeni ile seri işlemlerde kullanılamamaktadır. Kaplama kalınlığı 0.5-5 μm arasındadır. Bu sıçratma sırasında x ve γ ışınları kullanılmaktadır. [33]
Magnetron Sıçratma: Kaplama malzemesi ve ana malzeme bir mıknatıs üzerinde farklı kutuplara yerleştirilirler. Uygulana voltaj ile gerçekleşen manyetik hareket sonucu kaplama gerçekleştirilir.
Reaktif Sıçratma: Reaktif bir gaz ve inert bir gazın bir arada bulunduğu proses haznesinde kaplama malzemesinin sıçratılması ile kaplanacak yüzeyin üzerinde birikmesi sonucu oluşturulan kaplamadır.
PÜSKÜRTME İLE KAPLAMA
Püskürtme ile kaplama uygulamaları püskürtülen kaplama malzemesinin hızına veya sıcaklığına göre seçilmektedir. Genellikle plastikler yüksek sıcaklıklarda eridiğinden, yüksek sıcaklıklarda polimer matrisli kompozitler kullanılmaktadır. Genellikle karbon fiber takviyeli kompozitler, Polistiren, Poliamid, Polipropilen ve Polikarbonat-ABS karışımı kullanılmaktadır. Kaplama malzemesi olarak genellikle Alüminyum (Al) veya Bakır (Cu) malzemenin farklı formları kullanılır. Bu formlar püskürtme yönteminin çeşidine bağlı olarak tel veya toz olabilir. Proses sırasında ortaya çıkan sıcaklık mümkün oldukça düşük olmalıdır. Bu nedenle genellikle soğuk püskürtme uygulamaları tercih edilmektedir. [43]
SOĞUK PÜSKÜRTME İLE KAPLAMA
Bu yöntemde özellikle ergimiş bir kaplama malzemesi bulunmaması, sevk gazının soğuk kullanılabilmesi ve çevre dostu olması ısıl püskürtme prosesine göre avantajlarını oluşturmaktadır. Bu sistemlerin en büyük sorunu nozul tıkanmasıdır. Ana malzeme olarak çok geniş bir yelpaze bulunmaktadır. Ana malzemeye iletkenlik sağlama, onarma, korozyon koruması ve ısıl iletkenlik gibi özellikler kazandırılabilmektedir. [15] Soğuk püskürtme uygulamaları oldukça fazladır. Bunlar; eklemeli imalat, onarım, kaynak ve lehimleme, korozyon ve oksidasyon koruması, havacılık sanayi, medikal sanayi, savunma sanayi elektro iletken ve manyetik iletken malzeme sağlanması gibi alanlardır. [17] Pek çok parametre bu prosesi etkilemektedir:
Gaz sıcaklığı: Sıcaklığın artması olumlu sonuçlar vererek, porozite boyutu ve miktarını azaltır, boşlukların daha iyi dolarak kaplama kalitesini artırmaktadır.
Basıncın etkisi: İşleme göre uygun basınç değeri seçilmelidir. Basınç artışı poroziteyi boyut ve oran olarak artırır. Basın artışı ise parça ivmelerini düşürerek yine poroziteyi boyut ve oran olarak artırır.
Toz boyutunun etkisi: Toz boyutunun azalması farklı sıcaklıklarda farklı etkiler gösterse de genel olarak porozite boyutunu düşürmektedir.
Nozul geometrisinin etkisi: Bu parametre toz boyutuna, basınca ve gaz sıcaklığına göre farklılıklar göstermektedir. Uygulanan prosese göre incelenmeli ve uygun geometri seçilmelidir.
Soğuk püskürtme prosesi iki farkı yöntemle uygulanmaktadır. Bunlar; soğuk gaz dinamik sprey kaplama (SCDG) ve düşük basınçlı soğuk püskürtmedir.
Soğuk gaz dinamik sprey kaplama: Temel mantık püskürtme sırasında kullanılan gazın yüksek sıcaklığından ziyade yüksek kinetik enerjiye sahip olmalarıdır. Bu yöntem her ne kadar püskürtme yöntemi olarak kullanılsa da düşük proses sıcaklıkları avantaj sağlamaktadır. Gazın hızı 300-1200 m/s aralığında değişebilmekte ve ses üstü hızlara çıkılabilmektedir. Taşıyıcı inert gaz akımını genellikle azot veya helyum gerçekleştirmektedir. Bu taşıyıcı gazlar 700 ℃ gibi bir sıcaklıkta ön ısıtmadan geçirilerek gerekli yüksek ivmelenme için enerji doldururlar. Bu sıcak gazlar yakınsak ve ıraksak nozullerden geçirilirken genleşir ve ısısını kaybederek daha da fazla ivmelenir ve bu ivmeyi kaplama malzemesine aktarır. Bu yöntemde kritik hızın aşılması çok önemlidir. Kritik hızı aşamayan parçacıklar ya ana malzemeden sekerek geri döner veya ana malzemeyi erozyona uğratır. Bu yönteme yüksek basınçlı soğuk püskürtmede denir. [16]
Düşük basınçlı soğuk püskürtme: Bu yöntemde kullanılan sevk gazı basınçlı havadan oluşmakta ve püskürtme daha yakın bir mesafeden (5-15m) gerçekleştirilmektedir. SCDG yöntemine göre oldukça düşük maliyetli ve taşınabilir bir sistem olması en büyük avantajını oluşturmaktadır. Bu sistemlerdeki nozullerin ömrü daha uzun olmaktadır. Bunun nedeni daha düşük hızlarda nozullerden geçtiğinden aşındırma miktarının SCDG prosesinden daha düşük olmasıdır. [17]
ISIL PÜSKÜRTME İLE KAPLAMA
Isıl püskürtme kaplama yüksek sıcaklıklarda gerçekleşir. Bu yöntem ile Akrilonitril butadien stiren (ABS) Polisülfon (PSU), Polipropilen (PP), Polietilen (PE), Teflon gibi plastikler Alüminyum (Al), Bakır (Cu), Nikel (Ni), Altın (Au), Gümüş (Ag) ve Krom (Cr) gibi metallerle kaplanmaktadırlar. Kendi içinde çok farklı uygulama türleri bulunmaktadır. Bunlar:
Elektrik Ark Püskürtme
Bu yöntemde iki adet tel birbirlerine sürekli elektrik ark uygulayarak gerekli ısıyı sağlamaktadır. Isınan teller basınçlı hava ile birlikte kaplanacak ana malzeme üzerine püskürtülerek oluşturulmaktadır. Bu yöntemde çökelme hızının yüksekliği, yüksek bağ mukavemeti oluşması, kaplama maliyetinin düşük olması ve kaplamadaki oksit miktarının azaltılabilmesi diğer yöntemlere göre avantajını oluşturmaktadır. [14] Genellikle bağ kaplamasında çinko (Zn) kullanılmaktadır. Çünkü ergime sıcaklığı genellikle plastikler ile kaplama metalleri arasındadır ve iyi bir bağlayıcı görevi görmektedir. İşlem sırasında oluşan yüksek sıcaklıklardan dolayı plastiğin erimemesi için sıcaklık bir fan yardımı ile ortamdan uzaklaştırılır ve yüksek sıcaklık sadece kaplama yüzeyinde bağlanma sırasında meydana gelmektedir. Bu kaplamalar petrol-gaz endüstrisinde, elektronik endüstrisinde, tekstil, hayvancılık ve kimyasal işlemlerin olduğu ortamlarda kullanılmaktadır. [47]
SOL-JEL KAPLAMA
Bu işlem sırasında kullanılan kaplama proses başlangıcında sıvı fazda iken proses sonunda katı faza dönüşerek malzeme yüzeyini kaplamaktadır. Polimerlerin kaplanmadan önce yüzey temizliği önem arz etmektedir. Ne kadar temiz bir yüzey ile işlem gerçekleştirilirse kaplama malzemesinin yapışması da o kadar kaliteli olacaktır. Polikarbonat (PC) gibi polimerler kaplanmaktadır. Bu yöntemde proses sıcaklığının çok düşük olması ile enerjiden tasarruf edilmektedir. En önemli avantajlarından biri kaplamanın homojen bir şekilde gerçekleştirilmesi ve kaplama filminin mikro yapısının kontrol edilebilmesidir. Sıvı fazda bulunan kaplama malzemesi ortamla etkileşimde bulunmasa da sağlık açısından sorun çıkarabilmektedir. Bu nedenle gerekli koruyucu tedbirlerin sağlanması gerekmektedir. Bu kaplama yöntemi ile gözenekli yapıların elde edilebilmesi mümkündür. Kaplamalar çok katlı olabilir. Bu avantajlarının yanında dezavantajları da bulunmaktadır. Bunlar; malzeme maliyetinin fazla olması, Kaplama üzerinde karbon birikintiler kalması ve proses sırasında kaplama malzemesinin kaybının fazla olmasıdır. Sol-jel ile kaplamada şu yöntemler kullanılmaktadır: [46]
Döndürerek kaplama yöntemi
Daldırarak kaplama yöntemi
Püskürterek kaplama yöntemi
POLİMER KAPLAMALARA UYGULANAN TESTLER
Kaplama gerçekleştirildikten sonra belirli standartlara uyularak kaplamanın kalitesi kontrol edilmektedir. Bu testler şu şekilde sıralanabilir:
Kaplama tutunmasının tespiti
Kaplama ile 90 ⁰ açı yapacak şekilde tutunma tarağı ile iki defa çizik atılarak yüzey temizlenir. Özel bir bant çizik atılan yüzeye yapıştırılır. Bandın yapıştığı bölgede hava kabarcığı olmaması kaplamanın tutunmasının uygun olduğunu gösterir. Bu işlem ASTM D 3359-87 standardında gerçekleştirilmektedir.
Kaplamanın soyulma testi
Kaplanan numune yüzeyi 30 saniye süreyle 240 ve 320 kalınlıkta zımpara kağıtları ile zımparalanır. Test sonunda kaplamada çatlama ve yırtılma görülmemelidir. Bu işlem ASTM B 177-487 standartlarında gerçekleştirilir.
Kaplama çizilmesinin tespiti
Kaplama üzerine 0.1-10 N arasında bir kuvvet altında çizilir. Kaplama üzerindeki çizginin 24 saat içerisinde kaybolması istenir. Bu işlem ISO 4586-2 standardında gerçekleştirilir.
Kaplama kalınlığının tespiti
Kaplama kalınlığının tespitinde genellikle elektron mikroskobu kullanılır. Kaplanan parçadan numunelik kesitler alınarak gerekli işlemlerden (Parlatma, karbon kaplama vb.) sonra taranarak optimum kalınlıkta olup olmadığı kontrol edilmektedir. Bu işlem TS 3181 EN ISO 3497 standartlarına uygun olarak gerçekleştirilmektedir.
Kaplama renk ölçümü
Kaplama işleminde önce bir renk analizi gerçekleştirilir. Kaplama sonrası analiz tekrar gerçekleştirilir. Kaplama öncesi ve sonrası renkler karşılaştırılır.
Parlaklık ölçümü
Kaplama yüzeyine farklı açılarda ışınlar gönderilerek bu ışınların kaplamadan yansırken yapığı açılara bakılır. Bu işlem ASTM D 523-89 standardında gerçekleştirilir.
Ultraviyole dayanımı
Kaplama yapılan malzemeler uygun sürelerde standartlara uygun cihazlarda bekletilir. Kaplama ultraviyole ışına maruz kalmadan önce renk ve parlaklık ölçümleri gerçekleştirilir. Bu işlem ASTM D 3732-4414 standartlarına uygun olarak gerçekleştirilmektedir.
Sıcaklık değişimine dayanım
Kaplama belirli sıcaklıklarda optimum sıcaklıklarda tutulmaktadır. Test sonucunda kaplamada deformasyon, kabarma ve yırtılma olamaması gerekir. Bunun yanında renk ve parlaklık değişimleri de gözlenmelidir.
Isı dayanım direnci
Standartlara uygun sürelerde sabit sıcaklıkta bekletilmektedir. Test sonrası kaplamada kabarma, kalkma, renk ve parlaklık kaybı olmamalıdır.
Rutubet dayanımı
Belirlene standart sıcaklık ve bağıl nemde numune bekletilmektedir. Deney sonrası kabarma ve çatlama olamamalıdır. Kaplamanın tutunma tespiti ve parlaklığı kontrol edilmelidir. Bu işlem ASTM D2247-87 standardına uygun olarak gerçekleştirilmiştir.
Korozyon direnci
Kaplamalar uygun çözeltiler içerisinde belirli bir müddet bekletilmelidir. Çözeltinin bağıl nemi ve sıcaklığı kontrol altında tutulmalıdır. Bu işlem ASTM B 117-85 standardına uygun olarak gerçekleştirilmektedir.
METALLERİN POLİMER KAPLANMASI
Polimerler yüksek molekül ağırlıklı bileşiklerdir. Bazı polimerler çeşitli işlemeler ile iletkenlik özelliği kazandırılırlar. Bazı polimerler ise toz ve ergimiş olarak ana malzeme üzerine kaplanarak kullanılmaktadır.
ELEKTROSTATİK TOZ POLİMER KAPLAMA
Bu uygulama püskürtme metodunun bir çeşididir. Bir püskürtme tabancası, sprey kabini ve toz polimer kaplama malzemesinden oluşan bir sistemdir. Polimer tozlarına elektrik yüklemek için özel bir şarj kullanılmaktadır. Gerilim kaynağı ile birlikte üretilen akım püskürtme tabancası ucunda bulunan elektrota taşınarak manyetik alan oluşturulmaktadır. Tabancadan geçirilen hava ile birlikte polimer tozlar metala doğru püskürür. Bu sırada hava oluşan manyetik alan ile iyonize olarak polimer boyaya elektrik yükler. Bu sırada kaplanmak istenen ana metal malzeme topraklanmıştır. Elektriksel olarak yüklenen toz boya partikülleri topraklanan metale doğru akar. Ana metal malzeme üzerinde katma oluşturan toz polimerler 180 ℃ gibi bir sıcaklıkta pişirilerek eritilir ve yüzeye sabitlenir. Daha sonra kaplanmış metal soğumaya bırakılır. Bu sırada soğuyan polimer boya kaplama sertleşerek metal üzerinde sürekli bir tabaka oluşturur. Bu işlem genellikle yüksek yüzey kalitesi vermesi, enerji tasarrufu ve çevre dostu bir teknoloji olmasından dolayı tercih edilirken. En büyük dezavantajı ilk yatırım maliyetini ve kullanılan kaplama boyasının depolama maliyetinin yüksek olmasıdır. [19]

Polimerizasyon Kaplama
Bu aşamada polimer malzemeye iletkenlik özelliği kazandırılmaktadır. Genellikle ana malzeme olarak metaller tercih edilmektedir. İletken polimer pirol, anilin ve tiyofen monomerlerinin yükseltgenmesi ile elde edilmektedir. Kullanılan iletken polimerler poliprol, polianilin, poliasetilen, poli(p-fenilen) ve politiyofendir. [20] İletken polimerler ana malzemeye yüksek iletkenlik, yüksek kararlılık, korozyon ve oksidayon direnci gibi özellikler kazandırırlar. Çevreye etkisi bakımından bu yöntem sıvı bazlı polimerlerin ürettiği solvent maddesini ihtiva etmediğinden oldukça düşüktür. Polimerizasyon işlemi ile birlikte kopolimerler sentezlenmektedir. Polimer bir malzemenin iletken polimer hale getirilmesinde farklı metotlar kullanılmaktadır. Polimeri iletken hale getirme prosesine polimerizasyon denir. Bu işlemler şu şekilde sıralanabilir: [23]
Kimyasal polimerizasyon
Kimyasal polimerizasyon yöntemi bir çözücü içerisinde çözülen monomer yükseltgenme ve indirgenme aracı olan bir kimyasal tarafından polimerleştirilir. Basit ve ucuz olması en büyük avantajlarındandır. Ancak polimerleşme sırasında oluşan yükseltgenme işleminin kontrol edilememesi ve saf olmaması en büyük dezavantajıdır. İletken polimerin oluşumunda katalizörün büyük bir etkisi bulunmaktadır. [21]
Elektrokimyasal polimerizasyon
Proses sırasında yükseltgenme polimerin, ana malzeme (anot) üzerinde polimerleşerek birikmesi ve kaplamayı oluşturması ile gerçekleştirilir. Bu işlem elektroliz hücresinde gerçekleştirilir. Elektroliz hücresinde üç elektrotlu bir sistem kullanılmaktadır. Bu elektrotlar çalışma, karşıt ve referans elektrotlarıdır. Yöntem oda sıcaklığında gerçekleştirilebilmesi, akımı değiştirerek film kalınlığının ayarlanabilmesi, elektrot yüzeyinde kaplama yapılabilmesi, homojen bir film elde edilmesi ve en önemlisi reaksiyonların başlama ve bitişinin kontrol edilebilmesidir. [22] Proses başlangıcı direkt ve endirekt olarak gerçekleştirilebilmektedir. Endirekt başlamada ortama elektro aktif tuzlar kullanılırken direkt başlangıçta monomerler polimerleşmeyi kendi radikal katyonları ile gerçekleştirilirler. Polimerizasyon işlemi ne kadar hızlı gerçekleştirilirse o kadar avantajlı bir kaplama elde edilmektedir. Kimyasal yöntemlerle iletkenlik özelliği kazanamayan ketonlar, aldehitler, tiyoketonlar gibi monomerler elektrokimyasal yöntemlerle aktif hale getirilebilmektedir. Elektrokimyasal polimerizasyon prosesi; elektrot, elektrolit, uygulanan gerilim, sıcaklık, çözücü, ph ve monomer konsantrasyonuna bağlıdır. [24]
Piroliz polimerizasyon
Bu proses ile iletken organik polimerler elde edilmektedir. Bu uzun bir aromatik zincir oluşturmak için polimerin ısıtılması ve bu ısıtma sonucunda halojen, oksijen ve azot gibi maddeler uzaklaştırılır. Isısal uyarma ile birlikte serbest radikaller katyonları oluştururlar. Buradan elde edilen hidroliz ürünü toz, film ve lif olabilmektedir. [24]
Ziegler-natta katalizörlü polimerizasyon
Bu proseste katalizörler 4B-8B geçiş metalleri ve 1A-3A metallerden hazırlanır. Bu grup metaller birlikte kullanılarak organometalik bileşik oluşturur ve katalizör olarak kullanılırlar. Geçiş metallerine bağlanan moleküllerin oluşturduğu zayıf bağlar sayesinde tepkime isteği artar ve bu tepkime hızını artırır. Tepkimede katalizör görevini geçiş metalleri üstlenmektedir. Bu proseste kullanılan organometeller yeni nesil ve ileri malzemelerin geliştirilmesinde öncülük yapan bir teknolojidir. Bu proses ile biyouyumlu kaplamaların oluşturulmasında, yarı iletken parçacıkların üretilmesi, anorganik membranların geliştirilmesi, ince film üretimi ve nano yapılar oluşturulması ve silisyum bazlı malzemeler geliştirilmesi gibi uygulamalar yapılmaktadır. [24]
Kondenzasyon polimerizasyon
Bu proseste reaksiyon benzer veya farklı yapılardaki poli-fonksiyonel monomerlerin küçük bir molekül çıkarmasıyla oluşur. OH, COOH ve NH2 gibi fonksiyonel gruptan en az iki tane taşıyan monomerler esterleşme, amidleşme gibi reaksiyonlarla küçük moleküller çıkartırlar. Bu çıkan moleküller kondenzasyon polimerlerini oluşturur. Poliparafenilen polimeri kondenzasyon polimerizasyon yöntemi ile sentezlenmiştir. [24]
Emülsiyon polimerizasyon
Bu polimerizasyon işleminde birbiri ile karışmayan iki adet faz kullanılmaktadır. İşlemin gerçekleştirildiği ortamda su kullanılmaktadır. Emülsiyon yapıcı maddeler ile monomerler dağıtılır. Polimerizasyon başlatıcısı olarak suda çözünen bir madde kullanılır. [24]
Fotokimyasal polimerizasyon
Dış etkenlere bağlı olarak gerçekleştirilen polimerizasyon işlemidir. Bu dış etkenler bir ısı kaynağı ve bir de ışık kaynağıdır. Elde edilen polimerler baskı mürekkebinden teknolojik alanlara kadar geniş bir kulanım alanı bulmaktadır. Bazı tuzlar ve eterler fotokimyasal polimerizasyon ile gerçekleştirilebilir. Elde edilen tuzlar (diaril iyodonyum, triaril sülfonyum, N-alkoksi piridinyum vb.) ışığın dalga boyuna göre ayarlanarak polimerizasyon işleminin doğrudan veya dolaylı yoldan başlatılmasına olanak tanır. Tepkimenin başlatılmasında foto uyarıcılar kullanılmaktadır. İşlem süresi isteğe göre ayarlanabilmekte ve basamaklar kontrol edilebilmektedir. Bu kontrol bazı polimerizasyon işlemlerinde sertleşmenin sonradan yapılması gibi avantajlar göstermektedir. Kullanılan ışık ve ısı kaynağının kontrolü zincir uzunluğunun kontrolünü mümkün kılar. [25]
Kontrollü/yaşayan polimerizasyon
Moleküler yapı ve molekül ağırlığının kontrol edilebildiği polimerizasyon yöntemidir. Bu polimerizasyon yönteminde üç basamak bulunmaktadır. Bunlar; ayrışma-birleşme mekanizması, atom transfer mekanizması ve zincir transfer mekanizmalarıdır. Yeni çalışmalar ile birlikte çok farklı kontrollü polimerizasyon yöntemi geliştirilmiştir. Bunlar şu şekilde sıralanabilir: [25]
Atom transfer radikal polimerizasyon (ATRP)
Kontrollü halka açılma polimerizasyon (ROP)
Kararlı serbest radikal polimerizasyon (SFRP)
Tersinir katılmalı ayrışmalı zincir transfer polimerizasyon (RAFT)
TERMAL SPREY KAPLAMA
Metallerin polimerle kaplanması sırasında püskürtme yöntemlerinin kullanılması için özel bir tabanca kullanımı gerekmektedir. Çünkü polimerler düşük ergime sıcaklıklarından dolayı yüksek sıcaklıklı gazla temasları halinde erimekteydiler. Tabancanın uygun hale getirilmesi ve Polietilenin (PE) bulunması ile metaller kaplanmıştır. En önemli parametrelerden birisi püskürtme uzaklığı ve hava basıncıdır. Önceleri sadece dekoratif amaçlı gerçekleştirilen bu kaplamalar daha sonra mühendislik uygulamalarında oldukça önem kazanmışlarıdır. Kaplama sırasında polimerler genellikle toz hale getirilerek püskürtme tabancası tarafından ana malzemeye gönderilir. Polimer kaplamalar metalleri korozyondan korumaları, düşük sıcaklıklarda darbe direncini artırmaları ve boyadan oluşan solvent gibi uçucu zararlı maddelerin olmaması gibi avantajları bulunmaktadır. Termal püskürtmede kullanılan bazı toz ve tel polimerler şunlardır; Polietilen (PE), Etilen-Vinil alkol kopolimeri (EVOH), Polipropilen (PP), Vinil tozları (PVC, PVDF), Poli tetrafloraetilen (PTFE), Polyester, Nylon-Poliamid (PA), Akrilik (PMMA), Epoksi reçine (EP), Polikarbonat (PC), Polietereterketon (PEEK) ve Etinil vinil asetat (EVA). [45] [48]
CAM YÜZEY KAPLAMA
Mühendislik malzemesi olarak cam çok geniş bir kullanım alanı bulunmaktadır. Ancak cam malzemesinin kırılganlığı, çizilmesi, aşınması ve sıcaklık dayanımının düşük olması bu mühendislik malzemesinin kaplama yöntemleri ile birlikte yeni mekaniksel özellikler kazandırılarak ekstrem ortamlarda kullanılması mümkün olabilmektedir. Kaplama teknolojileri cama eklenmesi istenen mekaniksel özelliklere göre farklılıklar göstermektedir. Cam malzeme şu gibi amaçlarla kaplanmaktadır; dekor amaçlı, ısıl dayanım amaçlı, optik kullanım amaçlı, elektriksel özellikler amaçlı, mekanik ve kimyasal özellikler kazandırılması için kaplanmaktadır. Kaplama yöntemleri şu şekilde sıralanabilir: [26]
GÜMÜŞ KAPLAMA
Bu kaplama yöntemi ile cam malzemesinden ayna üretimi veya parlak yüzeyler oluşturmakta kullanılmaktadır. Bu proses cam levhaların öncelikle bir toz malzeme ile pürüzlülüğün giderilmesi ve temiz yüzey sağlanması sonrası ince bir gümüş çözelti dökülerek gümüşün cam üzerine indirgenmesi ile gerçekleştirilmektedir. [3]
VAKUM KAPLAMA
Vakum ortamında ince film üretim teknikleri kullanılarak cam üzerine sıçratma ile metal kaplama yöntemidir. Genellikle dekoratif amaçlı yapılmaktadır. Güneş panellerinden, gökdelenlere kadar pek çok yerde kullanılmaktadır.
SOL-JEL KAPLAMA
Sol-jel yöntemi ile cam içerisindeki silanol (SiOH) grupları ile jeldeki silanol gruplarının tepkimesi sonucu cam yüzeyinde siloksan (SiO-Si) bağları oluşturularak gerçekleştirilen kaplamadır. Bu kaplamada bağ ne kadar güçlü olursa kaplama dayanımı o kadar güçlü olur. Lekelere karşı koruyuculuğu yüksek bir kaplama elde edilir.
PÜSKÜRTME KAPLAMA
Uygun olarak hazırlanan çözeltinin nozullerden cam malzeme üzerine püskürtülmesi ile oluşturulan kaplamadır. Püskürtme sonucu cam üzerinde ince film tabakası oluşturulmaktadır.
SÜLFATLAMA İLE KAPLAMA
Cam malzeme yüzeyinin kükürt dioksit (SO2) buharı ile temas ettirilmesi sonucu cam yüzeyindeki sodyum oksit ile tepkimeye girmesi esasına dayanır. Bu tepkime sonucu cam yüzeyinde kükürt çiçeklenmesi adı verilen saydam bir katman oluşturulur. Bu kaplama sonucunda cam mukavemet, kimyasal dayanımını, aşınma ve yenim direnci artar.
ELEKTRO-İLETKEN KAPLAMA
Bazı uygulamalarda cam malzemenin elektriksel iletkenliği aranmaktadır. Bu özellik diğer yüzey kaplayıcıların yanı sıra kalay oksit ve indiyum oksit gibi belirli oksitlerle kaplama sonucu elde edilmektedir. Kaplama sonrası cam saydam kalır ancak bazı renkleri yansıtmaktadır.
YENİ NESİL KAPLAMALAR
Yüksek Sıcak Sentezleme
Bu yöntem kendinden gelişen bir reaksiyondur. Malzemenin yerinde sentezlenmesi ile yüksek performanslı seramik malzemenin plazma transfer ark işlemi ile birlikte oluşturulmasıdır. Bu yöntemde yüksek ürün saflığı ve düşük enerji ihtiyacı önemli avantajlardır. Plazma transfer yöntemiyle titanyum diborür (TiB2), titanyum karbür (TiC), TiB bileşiği ve demir fazları (Fe3Al, Fe2TiSi/γ, Fe/Ti5Si3) bu yöntem ile üretilmiştir. [27]
Plazma Transferli Termal Ark Tel Püskürtme (PTWA)
Isıl püskürtmenin bir türevi olan bu uygulama günümüzde motor silindir cidarlarında ısıl dayanımı artırmak, aşınma ve sürtünenin azaltılmasında kullanılmaktadır. Bu etkiler ile birlikte motor gücünün ve sistem veriminin arttığı gözlenmektedir. Bu iyileştirmelerin özellikle %0,8 karbon içeren bir çelik kaplama ile gerçekleştirildiğinde optimum iyileştirme sağlandığı gözlenmiştir. Bu teknolojinin otomotiv üreticileri tarafından denendiği de bilinmektedir. [28]
Mikro Ark Oksidasyon Kaplama
Mikro ark oksidasyon yöntemi Al, Ti, Zr, Mg gibi metaller üzerinde uygulanabilen bir prosestir. Bu yöntem ile malzeme korozyona, aşınmaya, hafiflik, termal etkilere dirençli ve elektrik yalıtkan özellikleri kazandırılmaktadır. Proses bir elektrolit banyo içerisinde yüksek voltaj altında ana malzeme üzerine anodik kaplama malzemesinin biriktirilmesi ile gerçekleştirilmektedir. Bu sırada kaplama malzemesi oksidasyona uğrar ve ana malzeme oksidasyona karşı koruma kazanmış olur. Bu yöntem kaplama kalınlığı, çevre duyarlılığı, kaplama tabakasının yapışması ve kaplama porozitesi açısından istenen sonuçları vermektedir. [29] Kaplamada kullanılan elektrolitler herhangi bir zehirli madde içermediğinden ve seyreltik olmaları bu elektrolitlerin üretim ve kullanımında kolaylık sağlamaktadır. Proseste kullanılan yüksek voltaj prosesin geliştirilmesinde büyük rol oynamaktadır. Bu proses farklı elektrot potansiyelleri ile gerçekleştirildiği gibi kaplanacak ana malzeme üzerinde oluşturulan elektriksel deşarjlar yardımı ile de gerçekleştirilebilir. Mikro ark oksidasyon prosesinin işlem basamakları şu şekilde sıralanabilir: [30]
Anodlama,
Anodlama + anodik çözme,
Anodlama + anodik çözme + oksijen çıkışı,
Mikro ark oluşumu ile kaplamanın gerçekleştirilmesi.
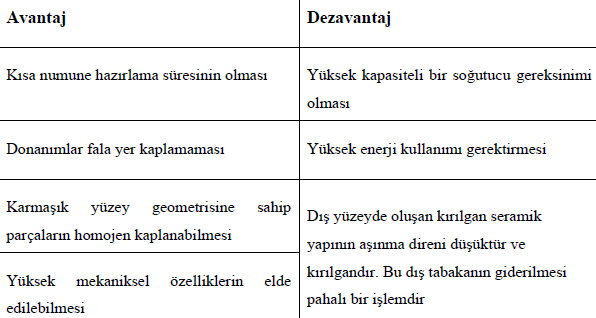
Biyomimetik Kaplama
Doğal mineralizasyonun doğada gözlemlenerek süreçlerinin kaplama proseslerinde uygulanmasına olanak sağlayan bir yöntemdir. Kaplama kristalin çekirdeklenme ve büyümesi ile gerçekleşmektedir. Bu durum kaplama kalınlığının kontrolünü mümkün kılar. İşlem suda gerçekleştirilir ve gözenekli poroziteli ana malzemenin homojen ve pürüzsüz kaplanmasını sağlar. Kaplama kalınlığı <30 μm’den küçüktür.
Termal Bariyer Kaplama
Yüksek sıcaklıklarda çalışan makine ve makine parçalarının ısıl dayanımlarını artırmayı amaçlayan yeni nesli bir kaplamadır. Bazı kritik makine parçaları da bu yöntemle kaplanarak üstün özellikler verilmektedir. Yüksek vakum altında gerçekleştirilmektedir. Katot metalden oluşurken anot iletken bir malzemeden oluşmaktadır. Bu iki zıt kutup arasında uygulanan yüksek gerilim ile birlikte metal atomları katottan kopartılarak anot malzemeye yönlendirilmektedir. [3] Türbinlerin yanma odaları, motor silindirleri, kanatlar ve uzay araçları gibi farklı uygulama alanları bulunmaktadır. Termal bariyer kaplama prosesi tek başına yeterli olmamaktadır. Ana malzemenin belirli şartları sağlaması kaplamanın daha verimli ve çalışma ortamında istenen kriterleri sağlaması sağlanmalıdır. Ana malzemede istenen özellikler şunlardır; yüksek mukavemet, yorulma dayanımı, sürünme dayanımı, erozyon ve korozyon direncine sahip olmalıdır. Bu koşulları sağlayabilecek ana malzemelerin süper alaşımlar olduğu görülmektedir. YMK yapıya sahip tek kristalli süper alaşımlar üzerinde denemeler devam etmektedir. Termal bariyer kaplama proseste kaplama malzemesi ile ana malzeme arasında bir bağlayıcı kullanılmaktadır. En verimli kaplama bağlama metali olarak MCrAlY ve kaplama malzemesi olarak YSZ kullanılarak oluşturulmaktadır. Termal bariyer kaplama yönteminde hasara yol açan etkenler şunlardır: [32]
Oksidasyon
Korozyon (Sıcak-Elektrokimyasal)
Erozyon
Termal şok
Kimyasal ve termomekanik hasarlar
Sürtünme, aşınma ve yorulma
CMAS (Ca-Mg-Al-Si) atağı
Elektroforetik Kaplama
Yüklü parçacıklara zıt yönde elektrik yük uygulanarak hızla ana malzemeye çarparak kaplamanın gerçekleştirildiği yöntemdir. Düşük maliyetli olmasının yanında karmaşık şekil ve parçaları kolaylıkla kaplanmaktadır. Kaplama kalınlığı 0.1-2 μm arasında değişmektedir.
Darbeli Lazer Biriktirme Kaplama
PLD sistemi lazer demetinin optik yönlendirme sistemleri ile ana malzemeye çarptırılarak gerçekleştirilir. Bu yöntem plazma püskürtme prosesinin farklı bir uygulamasıdır. Sistem lazer kaynağı, vakum odası, optik bileşenler e otomatik kontrol bileşenlerinden oluşmaktadır. PLD kaplama ile çok yoğun ve ince kaplamalar gerçekleştirilmektedir. Kaplama ve ana malzeme arasında çok güçlü bir yapışma meydana getirmektedir. Lazer demetleri yüksek sıcaklık oluştururlar. Hidroksiapatitin (HAP) ince filmleri oluşturmada kullanılan bir yöntemdir. [37]
Askeri Gizleme Kaplamaları
Günümüzde savunma sanayinde kullanılan ileri teknoloji roket, uçak, helikopter gibi ekipman ve makinelerin radarda görünürlüğünü düşürmek için çalışmalar devam etmektedir. Hayalet teknolojisi olarak da adlandırılan düşük tespit edilebilirlik tamamen gizlenme üzerine değil hedefin geç tespit edilmesini sağlayan bir teknolojidir. Bunun için ekipman veya makineden yansıyan sinyal gücünün radar alıcı gücünden düşük seviyeye indirilmesi gerekir. Bunun için farklı uygulamalar bulunmaktadır. Malzemenin şekillendirmesi ile gelen sinyali farklı açılarda yansıtabilir, malzeme boya ile kaplanabilir veya malzeme radar soğurucu malzeme (RSM) ile kaplanabilir. Radar soğurucu malzemeler içerisinde bulunan karbon ve ferrit parçaları ile radar sinyalinin kendi içinde yansıtarak zayıflatmaktadır. RSM kaplamaların etkin kullanılmasında radar dalgalarının bant genişliği önemli rol oynamaktadır. Dar bant genişliğindeki dalgalarda kısmi kaplamalar işe yararken geniş bant aralığında görevlerini yerine getirememektedir. Ayrıca bu kaplama malzemeleri her frekansta gelen sinyalleri soğuramadıkları gibi hava aracının veya ekipmanın kalınlık ve yoğunluğunu artırmaktadır. Geniş bant aralıklarında radar kesit alanını (RKA) düşürmek için çalışmalar yapılmaktadır. Radar soğurucu malzemeler ile birlikte plazma kullanımı görülmektedir. [38] Radar soğurucu malzemelerin tasarımında dikkat edilmesi gereken parametreler bulunmaktadır. Bunlar; rezonans frekansı (f0), bant genişliği (Δf), yansıma katsayısı (𝛤), katman kalınlığı (H) ve düzlem dalga geliş açısı (θ, ϕ) gibi parametrelerdir. Radar soğurucu malzemelerin kaplanmasında, kullanılacak kaplama malzemesine göre uygun kaplama yöntemi seçilmektedir. Genel olarak ince film üretim teknikleri, sol-jel kaplama tekniği veya kimyasal banyo ile kaplama metotları kullanılmaktadır. Kullanılan kaplama malzemeleri yumuşak metaller, karbürler, iletken polimerler, erime sıcaklığı düşük metaller, metal oksitler ve elmas benzeri karbonlar kullanılmaktadır. [39]
Hidrofobik Kaplamalar
Bu kaplama sol-jel yöntemi ile gerçekleştirilmektedir. Metal malzemelerin mükemmel kimyasal dirence sahip olmaları, nem ve ortam şartlarından etkilenmeyen bir kaplama ortaya çıkmaktadır. Kaplama malzemesi olarak Floropolimer ve Silikon olarak polimer bileşenler kullanılmaktadır. Ana malzeme olarak dökme demir, alüminyum ve titanyum gibi metaller kullanılmaktadır. Kaplama öncesinde ana malzeme yüzeyi kumlama ve kimyasal çözeltiler ile temizlenmeli, kaplamanın mikro yapışmalarda istenen düzeyde olması istenir.[49] Kaplanan yüzeylerin hidrofobikliği kaplama üzerine damlatılan su damlasının yüzey ile yaptığı açı ile belirlenmektedir. Ayrıca bu kaplama ile ana malzemeye aşınma direnci sağlanmaktadır. [50]
Kendini Onaran Kaplamalar
Bu kaplamalar organik canlıların çevre şartlarına gösterdiği tepkiler gibi dış müdahalelere ihtiyaç duyulmaksızın, darbe gibi etkenlerden oluşan çizik veya çatlak gibi hasarları kendi kendine onarmalarıdır. Bu kaplamalar özellikle dinamik yükler alında çalışan parçalarda öne çıkmaktadır. Bu kaplamalarda Epoksi reçineler hem matris bileşeni olarak hem iyileştirici ajan olarak görev yaparlar. İyileştirici ajanlar mikro kapsüllere hapsedilmektedirler. Mikro kapsüllere aktarılan epoksi reçinelere daha sonra kürleme işlemi gerçekleştirilir. Kaplama herhangi bir çizik veya çatlağa maruz kaldığında Epoksi reçine dolu mikro kapsüller patlayarak oluşan hasarı giderirler. Bu kaplamalarda en önemli parametreler mikro kapsüllerin boyutu ve kabuk kalınlığıdır. [51]
DENEYSEL KAPLAMA AŞAMALARI
Kaplamanın kalitesini belirleyici çok farklı unsurlar bulunmaktadır. Bu unsurlar kaplama yöntemi, sıcaklığı, kullanılan ekipman kalitesine kadar çok geniş bir yelpazede incelenebilir. Ancak kaplamalar belirli değerlendirmelere tabii tutulabilir. Bunlar; yüzey pürüzlülüğü, sertlik deneyi, korozyona ve oksidasyona uğratarak etkilerin incelenmesi gibi etkenlere bakılarak kaplama kalitesi belirlenebilir: [40]
Numunenin hazırlanması: Uygulanacak kaplama prosesine göre hazırlama işlemi gerçekleştirilmektedir. Proses durumuna göre Numune seçimi gerçekleştirildikten sonra yüzey pürüzlülüğü, yüzey hazırlama işlemleri -ki bu işlemler genellikle kimyasal metal kaplama yöntemlerine uygulanır- veya uygulanacak kaplamanın hazırlanması işlemlerini içerir. Kaplamanın hazırlanması elektrolitin hazırlanması, toz malzemenin hazırlanması veya uygun kaplama telinin tedarik edilmesi gibi işlemleri içermektedir.
Kaplama kalınlığı: Kaplama sonucunda kaplama kalınlığı uygun cihazlarla ölçülerek kaplama kalitesi kontrol edilmektedir. Kaplama kalınlığı optik cihazlarla, aşındırıcı cihazlarla veya sertlik ölçüm yöntemleri ile kontrol edilebilmektedir.
Yüzey ölçümleri: Yüzey kalitesi mikro ve makro çizik testleri, nano sertlik cihazları ile kontrol edilebilmektedir. Yüzey tarama cihazları ile birlikte kaplama öncesi ve sonrası malzemenin yüzey taraması gerçekleştirilerek pürüzlülük ölçülerek kaplama kalitesi kontrol edilmektedir.
Yüzey deneyleri: Kaplama sonrası kaplama kalitesinin farklı deneylerle ölçülendirilmesi çok farklı deneylere tabi tutularak gerçekleştirilir. Bunlar; çizme ve kareleme deneyi, eğme deneyi, eğeleme deneyi, kesme deneyi, ısıl şok deneyi ve sıcak su deneyi gibi deneyleri içermektedir.
Kaplamanın mikroskobik incelenmesi: Genellikle parçadan alınan örnek numunelerin mikroskop üzerinde incelenmesi ile kaplama kalitesinin tayin edilmesini içermektedir.
SONUÇ
Kaplama teknolojisinin geldiği noktada, kaplama uygulamalarının sadece tek bir ana malzeme üzerine uygulanamadığı, farklı ana malzemelerin tek bir kaplama yöntemi ile kaplanabildiği görülmektedir. Bu kaplama yöntemlerini sınıflandırmada zorluk doğurmaktadır. Önümüzdeki yıllarda kaplama teknolojilerinde oldukça fazla gelişme olacağı açıktır. Kaplamalar gündelik yaşantımızda kullandığımız elektronik cihazlardan dekoratif eşyalara, otomobillerden uçaklara, uzay araçlarından camlara kadar çok farklı noktalarda bulunmaktadır. Sadece burada kullanıldığı alanlar bile ne kadar çeşitli uygulamalarda kullanıldığını göstermektedir. Araştırma ve geliştirme aşamasındaki pek çok yeni kaplama teknolojisinin ülkemize kazandırılması oldukça önem arz etmektedir. Kaplama teknolojilerinin üretilmesinde ve ülkemize kazandırılmasında dışa bağımlılığın azaltılması ve çevreye duyarlılığın yüksek olmasına dikkat edilmelidir. Ülkemizde metal ve plastik kaplamalarda oldukça fazla yol alınsa da yeni nesil kaplamalarda, literatür araştırmalarında Türkçe kaynak kıtlığı bulunmaktadır. Bu yeni nesil kaplama alanında akademik çalışmaların artması gerektiğine işaret etmektedir.
KAYNAKÇA
[1] ALTINIŞIK E. ve ENGİN S., 2011, Sanayide Daha Etkili Bir Çevre Yönetimi İçin Temiz Üretim, Milli Prodüktivite Merkezi Yayınları, 1. Baskı, Ankara, 978-975-440-383-1.
[2] BOLAT, TİMUR, KELEŞ, 02.09.2013, Çinko-Alüminyum Alaşımından Üretilmiş Dokum Parçalarının Korozyon Direncine Bakır Kaplama Proseslerinin Etkisi, İstanbul Teknik Üniversitesi, Metalürji ve Malzeme Mühendisliği Bölümü
[3] YÜKSEL, KÜBRA, 05.2012, Ligand Fonksiyonlu Polimer Mikro Küre Yüzeylerine Kendinden Tohumlamalı Elektrolizsiz Kaplama Yoluyla Metal Kaplanması, Yüksek Lisans Tezi, Fen Bilimleri Enstitüsü/İstanbul Teknik Üniversitesi.
[4] YONAR, KENAN, 1979, Galvano Teknik, Milli Eğitim Basımevi, 1. Baskı, İstanbul.
[5] BERK, VEDAT, 2004, Yüzey İşlemler Teknolojileri 1.
[6] SARAÇ, SEZAİ, 1995, Metal Kaplanma ve Elektrokimyasal Teknolojiler, 1. Baskı, İTÜ Fen Edebiyat Fakültesi, Çağlayan Kitapevi, İstanbul.
[7] AKMAN, BURCU, Sıcak Daldırma Galvanizle Sürdürülebilir Korozyon Koruması, 6. Çelik Yapılar Sempozyumu, 11 Aralık 2015 Eskişehir, GALDER, 146-148.
[8] PEKTAŞ, İBRAHİM, 2018, Galvanizcinin El Kitabı, 10-12
[9] KÖKSAL ve PASİNLİ, 2009, Sıcak Daldırma Yöntemi ile Alüminyum Kaplanan Çelik Malzemelerde Yüksek Sıcaklık Oksidasyonunun İncelenmesi, DEÜ Fen ve Mühendislik Dergisi, 11(31).
[10] ÖZKUL, FATİH, 2019, Elektroliz Yöntemi ile Metal Kaplama Teknolojisinde İş Sağlığı ve Güvenliği, Yüksek Lisans Tezi, Fen Bilimleri Enstitüsü/Gazi Üniversitesi.
[11] SÖNMEZOĞLU, KOÇ ve AKIN, 2012, İnce Film Üretim Teknikleri, Erciyes Üniversitesi Fen Bilimleri Enstitüsü Dergisi, 28(5), 389-401.
[12] AYTAÇ ve MALAYOGLU, 2018, Fiziksel Buhar Biriktirme Yöntemlerinden PVD ve JVD/DVD İnce Film Kaplamaların Karşılaştırılması ve DVD Kaplama Teknolojisinin Endüstriyel Uygulamaları Üzerine Kavramsal, Akademik ve Teorik Bir Analiz, Savunma Bilimleri Dergisi, 17(1), 132-162, 1303-6831.
[13] KARADENİZ ve diğerleri, 2011, Toz Metal Püskürtme Yöntemi ile Boru İç Yüzeylerinin Kaplanması ve Karakterizasyonu, 6. Uluslararası Toz Metalürjisi Konferansı ve Sergisi, 5-9 Ekim 2011, Orta Doğu Teknik Üniversitesi/Ankara.
[14] ÖZEL SERKAN, 2013, Yüzey Kaplama İşlemlerinde Kullanılan Isıl Püskürtme Yöntemleri, BEÜ Fen Bilimleri Dergisi, Bitlis Eren Üniversitesi
[15] ÜSTEL ve ALTUNCU, Soğuk Sprey (Cold Spray) Teknolojisi ve Uygulama Alanları, Türk Mühendis ve Mimar Odaları Birliği, Metalürji Mühendisliği Odası
[16] KARAOĞLANLI ve diğerleri, 2013, Soğuk Gaz Dinamik Sprey (CGDS) Kaplama Teknolojisi ve Uygulama Alanları, APJES I-I, Bartın Üniversitesi, 20-27.
[17] TEKİN ve diğerleri, 2021, Soğuk Püskürtme Teknolojisi ve Uygulamaları, Mühendis ve Makine Dergisi, 62(702), 106-150, 10.46399/muhendismakina.798947.
[18] ÜSTEL ve ALTUNCU, 2013, Termal Sprey Kaplama Sektöründe Son Gelişmeler, Sakarya Üniversitesi.
[19] ÖZDİLLİ, ÖZGÜR, 2018, Polimer Kaplı Metal Sacların Derin Çekme Davranışlarının İncelenmesi, Doktora Tezi, Fen Bilimleri Enstitüsü/Hitit Üniversitesi.
[20] KORSACILAR, DUYGU, 2012, Metalik İmplant Malzeme Yüzeylerinin Elektropolimerizasyon Yöntemi ile Sentetik Hidrojel Polimerle Kaplanarak Biyouyumluluğun Artırılması, Yüksek Lisans Tezi, Fen Bilimleri Enstitüsü/Dokuz Eylül Üniversitesi.
[21] YAKAR, ELEM, 2006, Elektropolimerizasyon Yöntemiyle Polipirol ve Polianilin ile Kaplanmış Alüminyumun Asidik Korozyonunun Önlenmesinde Farklı Anyonların Etkileri, Yüksek Lisans Tezi, Fen Bilimleri Enstitüsü/Kocaeli Üniversitesi.
[22] KARACİF ve diğerleri, 2010, Alüminyumun İletken Polimer ile Kaplanması ve Kaplama Mikroyapısına Korozyonun Etkisinin İncelenmesi, Gazi Üniversitesi Mühendislik Mimarlık Fakültesi Dergisi, 25(2), 235-241.
[23] ÖZŞAHİN ve TOLUN, Temmuz 2010, Yüzey Kaplaması ve Destek Katman İlavesinin Alüminyum Levhaların Balistik Performansına Etkisi, Havacılık ve Uzay Teknolojileri Dergisi, 4(4), 41-50.
[24] TOPTAŞ, NEVİN, 2006, Anilin ve Poliakrilonitril Kullanarak Kimyasal Polimerizasyon Yöntemi ile İletken Kompozit Lif Hazırlanması, Yüksek Lisans Tezi, Fen Bilimleri Enstitüsü/Ankara Üniversitesi, 18-25.
[25] ATMACA, HAFİZE, 2019, Rop ve Fotokimyasal Polimerizasyon Yöntemlerinin Birleştirilmesi ile PLLA-PMMA ve PLLA-PCHO Blok Kopolimerlerin Sentezi, Fen Bilimleri enstitüsü/Harran Üniversitesi.
[26] SARICAOĞLU ve KARASU, 2018, Cam Yüzey Kaplama Teknolojileri, El-Cezerî Fen ve Mühendislik Dergisi, 5(2), 475-500.
[27] AY, MEHMET, 2017, AISI 4140 Çelik Malzemenin Yüzey Özelliklerini Geliştirmek İçin Yenilikçi Bir PTA Yöntemi, Doktora Tezi, Fen Bilimleri Enstitüsü/ Eskişehir Osmangazi Üniversitesi.
[28] HÜRPEKLİ, MERSİN, 2013, Isıl Püskürtme Kaplamanın Motor Performansı ve Silindir Boşluğu Üzerindeki Etkisi, Yüksek Lisans Tezi, Fen Bilimleri Enstitüsü/İstanbul Üniversitesi.
[29] YILMAZ, MUSTAFA, 2018, Mikro Ark Oksidasyonda (MAO) Elektriksel Proses Parametrelerin Alüminyum Esaslı Malzeme Kaplamalarına Etkisi, Doktora Tezi, Fen Bilimleri Enstitüsü/Gazi Üniversitesi.
[30] YURCİ, YILMAZ, 2019, Mikroark Oksidasyon (MAO) Yöntemi ile Kaplanmış NiTi Alaşımının Korozyon Davranışının İncelenmesi, Fen Bilimleri Enstitüsü/Atatürk Üniversitesi.
[31] İNÇAL, EMİR, 2007, PVD Yöntem ile Kaplanan HSS Takım Çeliklerinin Karakterizasyonu ve Aşınma Dayanımının İncelenmesi, Yüksek Lisans Tezi, Fen Bilimleri Enstitüsü/İstanbul Teknik Üniversitesi.
[32] ALTAN, ELİF, 2019, LİF, 2019, Termal Bariyer Kaplamaların (TBC) Mikroyapısal ve Elektrokimyasal Korozyon Davranışlarının İncelenmesi, Yüksek Lisans Tezi, Fen Bilimleri Enstitüsü/Bartın Üniversitesi.
[33] DÜDEN, ENES, 2018, Titanyum Plakaların Aerosol Kaplama Yöntemi ile Hidroksiapatit Kaplanması ve Karakterizasyonu, Yüksek Lisans Tezi, Fen Bilimleri Enstitüsü/Anadolu Üniversitesi.
[36] YEŞİLÇUBUK, ALPER, 2002, Reaktif DC Magnetron Sıçratma Tekniği ile n-Tipi Silisyum Altlık Üzerine Bakır Oksit İnce Film Biriktirme, Yüksek Lisans Tezi, Fen Bilimleri Enstitüsü/İstanbul Teknik Üniversitesi.
[37] YURTCAN ve EKMEKÇİ, 2020, Darbeli Lazer Biriktirme (PLD) ile Ti-6Al-4V Üzerine Hidroksiapatit (HAP) İnce Filmlerinin Hazırlanması¸ NÖHÜ Mühendislik Bilim Dergisi, 9(1), 598-605.
[38] KILIÇ, ÖZKAN, 2017, Askeri Uygulamalar için Plazma Kaplamaların Tasarımı, Yüksek Lisans Tezi, Hacettepe Üniversitesi.
[39] ÖZER, ALİ, 2018, Geniş Bantlı Yeni Bir Radar Soğurucu Yapı Tasarımı, Yüksek Lisans Tezi, Hacettepe Üniversitesi.
[40] MATİK ve ÇATIK, 2005, Toz Metalürjisi ile Üretilmiş Demir Esaslı Parçalarda Asidik ve Bazik Akımsız Nikel Çözeltilerin Kaplama Kalitesine Etkisi, Gazi Üniversitesi Mühendislik Mimarlık Fakültesi Dergisi, 20(2), 239-246.
[41] GÖKKURT, TOLGA, 2007, Farklı Yöntemlerle Kaplanan Termoplastiklerin Mekanik Özelliklerinin Değerlendirilmesi, Yüksek Lisans Tezi, Fen Bilimleri Enstitüsü/Marmara Üniversitesi.
[42] ÖZTOP, ESEN, 2006, Fiziksel Buhar Biriktirme Yöntemi ile Kaplanan Polimer Malzemelerin Özellikleri, Yüksek Lisans Tezi, Fen Bilimleri Enstitüsü/İstanbul Teknik Üniversitesi
[43] ZHOU ve diğerleri, Preparation of Metallic Coatings on Polymer Matrix Composites by Cold Spray, Surface & Coating Tecnology 206 (2011), 132-136.
[44] WOLFF ve diğerleri, Coatings on Plastics With The PICVD Technology, Thin Solid Films 442 (2003), 107-116.
[45] ZAĞLI, MUHAMMET, 2010, Alev Sprey Yöntemiyle Polimer Kaplamaların Üretimi ve Karakterizasyonu, Yüksek Lisans Tezi, Fen Bilimleri Enstitüsü/Sakarya Üniversitesi.
[46] BOZTOPRAK ve diğerleri, 2007, Sol-Jel Tekniğiyle Kaplanan Polikarbonatların Fiziksel Özelliklerinin İncelenmesi, 8. Uluslararası Kırılma Konferansı, Marmara Üniversitesi, İstanbul, 330-337.
[47] NİGAM ve diğerleri, Study of Various Aspect of Copper Coating on ABS Plastic by Electric Arc Spraying, Mechanical Engineering Department, National Institute of Technology, Hindistan, 5 (2018), 8446-8453.
[48] ALTUN, OSMAN, 2011, Alev Sprey Yöntemiyle Etilen Vinil Asetat Kaplamaların Üretilmesi ve Karakterizasyonu, Yüksek Lisans Tezi, Fen Bilimleri Enstitüsü/Sakarya Üniversitesi.
[49] MEHMETALİOĞLU ve diğerleri, Nano TiO2 Dolgulu Polimer Esaslı Hidrofobik Kaplamanın Yüzey Özelliklerinin İncelenmesi, Sakarya Üniversitesi Fen Bilimleri Enstitüsü Dergisi, 21(2), 2017, 77-81
[50] KARAKURT ve diğerleri, 2019, Floro Polimer Esaslı Malzeme ile Kaplanmış Dökme Demir Plakaların Hidrofobikliğinin ve Aşınma Direncinin İncelenmesi, ISAS 4(1), 472-475, Ankara, Türkiye.
[51] LİU ve diğerleri, Preparation of Epoxy Microcapsule Based Self-Healing Coatings and Their Behavior, Surface & Coatings Technology 206 (2012) 4976–4980.
Comentarios